
What is metal casting? How does metal casting work? Metal casting is a manufacturing process that produces a coherent and solid object through pouring liquid metal into a mold. This mold provides the shape of the final product. Metal casting is one of the few materials processes that are considered to be both an art and a science.
The process includes heavy manual labor, which makes it more costly than other methods, but can be worth it for large production runs. Like any process involving molten metals, there are risks for fires and burns associated with hot surfaces and molten metal in proximity to combustible materials, as well as chemical risks from handling bismuth trioxide resin or sulfur in contact with water or acid; however, proper safeguards can prevent such accidents from happening.
In this article, we are going to explore metal casting for you. What is metal casting? How does metal casting work?
What is metal casting?
Metal casting is defined as the process in which molten metal is poured into a mould that contains a hollow cavity of a desired geometrical shape and allowed to cool down. When the molten metal solidifies, the mold is opened and the metal casting is removed.
The casting process is used for creating complex shapes that cannot be made by casting or by simply pouring molten metals into molds. Some of the main reasons to use it include the ability to produce large quantities of identical products and to create objects with fine surface details that could not be achieved any other way.
Casting is one of the oldest manufacturing processes known to man. It is the oldest way of making metal objects and has been in use for at least 4,000 years. Metal casting is one of the few materials processes that are considered to be both an art and a science.
To make a product, the master die is created first. It is a mold that contains a hollow cavity of a desired geometrical shape. The shape of the cavity depends on what kind of object you are going to cast. For example, if you want to create bullets, you will need to make gunpowder bullets molds, whereas if you need wide tiles for flooring you will need wide tile molds.
A pattern is one of the tools used to create a master die. The moulds are made with patterns, which are essentially flat pieces of material that have been embossed with the design you want your final object to have. Patterns can be made from a variety of materials such as wax, clay, plastic or steel.
Metal casting is an extremely expensive process so many companies do not make their own patterns anymore. Instead, they buy them from other manufacturers and use them to reproduce a castings.
The design and creation of moulds includes many different processes including pattern making, core making, lost-wax casting and sand casting etc.
How does metal casting work?
How does metal casting work? Let’s Move!
We will be looking at steps involved on how metal casting is done and how its works. These steps includes:
- Making Patterns:
The first step in metal casting is making patterns. The main idea is to create a master die in one piece. This is that shape you want the final product to have. A pattern can be anything from wax or clay to a steel slab.
When the mould is completed, it is called a pattern then, which means the mould was already created and castings are made from it. There are many different ways of creating pattern, but there are two main techniques used: lost-wax casting and sand casting.
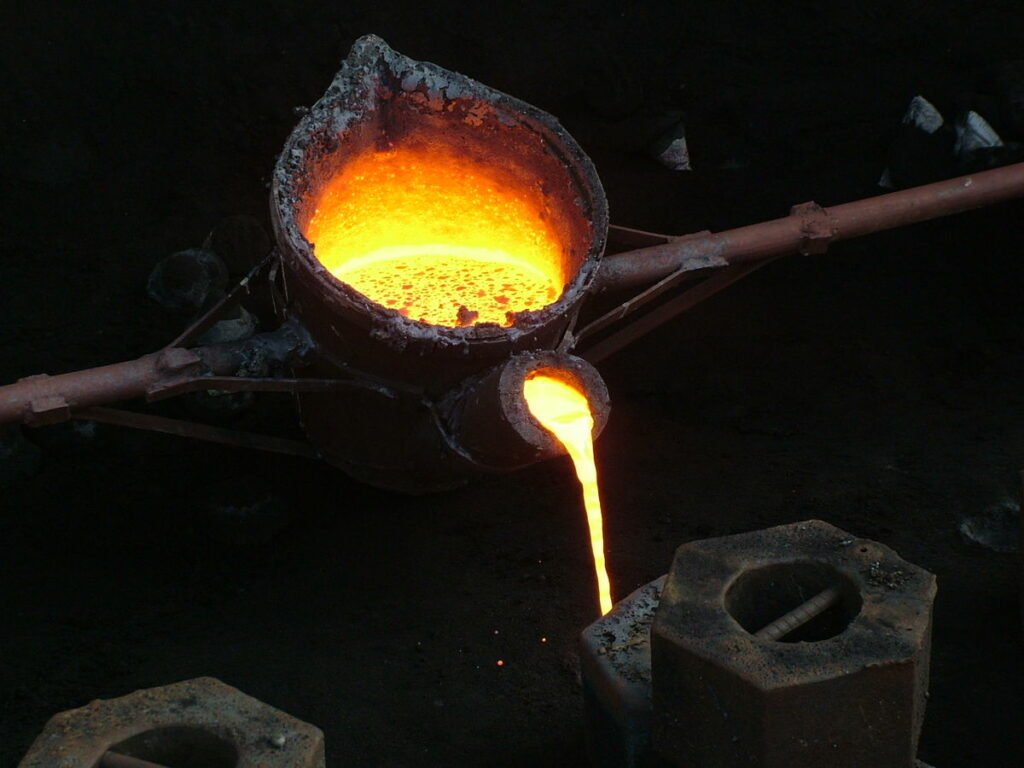
- Core Making:
The core making process is used to make the moulds of low-volume production. In this method, a hardened plastic core is filled with molten metal and then shaped into a hollow mold. This method produces molds which are more complex than sand casting, but less complex than lost-wax casting since it does not require the use of expensive high grade metals for the molds.
This method is used for creating molds for products with high detail such as equipment, tools and utensils etc.
The lost-wax casting process is a temporary mould which allows you to create molds for production lots of items. Welded iron rods are used to form all of the pattern parts, except the one that will be used as a mould. The rods are welded together and the gaps between them are filled with molten wax, which hardens when it cools.
This method is commonly used because it can be done quickly, and it produces molds with high detail from small amounts of material. Often times we don’t need molds for making hundreds or thousands or products. In those cases, the best option is sand casting, but lost-wax casting can be used as well.
The sand casting process is a permanent mould which is made out of a fine grained powder. This powder acts as the material for creating the pattern. The mould core for making sand castings uses a strong clay as its base and has a relatively small hole in the centre to hold water and resin that will fill in sand particles and create the final mould.
The sand casting process produces molds with lesser detail but can work with much less material than lost-wax casting can since it does not require grinder to create patterns, only mills to put materials into form.
- Pouring Metal:
Metal is poured into the mould when it is cool. The mould is then opened and the final product is removed. There are several ways to pour metal into a mold. Metal casting methods include: plough casting, direct casting, gravity casting and rotating pouring method.
The plough casting method is one of the oldest metal casting process and involves using a funnel to pour molten metal into molds. In this method, once the mould has been filled with molten metal and cooled, it can be opened without damaging it since there will not be any material left in it.
With direct pouring process, the molten metal flows from a bowl directly into moulds. This process uses less material than other casting methods, but the problem with this method is that the mold itself cannot be reused, which means that if any flaws affect the finished products, they have to be destroyed.
Gravity methods are used to pour molten metal into large molds. This process is typically used to make large items such as gears, engine parts and a lot of other industrial parts. The main idea is that once the mould has been filled with metal it will sink down in a pouring bowl. When cooled down it can be removed from the pouring bowl using air pressure and other techniques.
The rotating pouring method is used for casting small objects and requires two people to work together at two stations.
Read Also: Metal Roof Systems: Standing Seam Vs. Screw Down Panels
- Removing the Pattern:
After the pattern is removed, it will be used to create more molds. If you want to reuse the pattern, it will be kept in a container filled with oil or resin. - Final inspection and Quality Control:
Finished products will then be sent for final inspection for flaws and defects that may have been missed earlier. Small defects can be fixed by grinding part of product, but large flaws can cause major problems with its functionality and thus, the whole mould has to be scrapped.
Advantages and disadvantages of metal casting
Advantages
The advantages of metal casting include:
- The production of the product is quicker than other ways of manufacturing.
- It scales up rapidly as it is not limited in size.
- The product has less risk for defects which can be repaired by grinding and reusing the pattern.
- The product is manufactured in larger volumes because one mould can be used multiple times without having to create a new one from scratch each time.
- The casting objects have high compressive strength.
- All material can be cast.
- The process yield of the casting is high, and the liquid metal consumption is reduced, generally saving 15 to 30%.
Disadvantages
As we all know, what has an advantage also has some disadvantages, now we have looked into how metal casting does work and its advantages, lets get into the disadvantages of metal casting.
The disadvantages of metal casting include:
- High production cost.
- Casting defects involves in this process.
- High-maintenance parts and equipment must be used during the production process.
- The metal type is airtight and has no retreat, which may cause defects such as insufficient washing of the casting, cracking or white cast iron parts.
- It is not economical for mass production.
- Compared with forgings of the same size and shape, the intrinsic quality of castings is weaker, and the load-bearing capacity is less than that of forgings.
- Part size and material choices depend on the casting process chosen. For instance, only non-ferrous metal can be used for permanent mould castings.
Conclusion
How does metal casting work? Metal casting is a very important process in the manufacturing industries. It has the ability to create objects that are durable and can withstand a lot of stress without breaking. One of its main purposes is to protect the environment by preventing wastage of raw materials. A lot of people see this process as too complicated, but it isn’t as hard as it might seem to be.
All it takes is time, effort and patience in order to achieve the desired result. It may seem difficult at first, but once you understand what you need to do, everything else will fall into place. This process is widespread in the manufacturing industries, which are mostly metal and plastic industries.
Small to medium sized companies, such as small manufacturers, can also benefit from this process. It helps them produce parts faster and cheaper. Manufacturing companies can benefit from using this process because it produces high quality products that can last for a long time without breaking or wearing out.
It also provides the company with an option to recycle the product into another one if necessary. Investing in metal casting is worth considering because it will provide you with a lot of benefits in the future, such as a stronger, more durable product and increased production of your company’s goods and services.
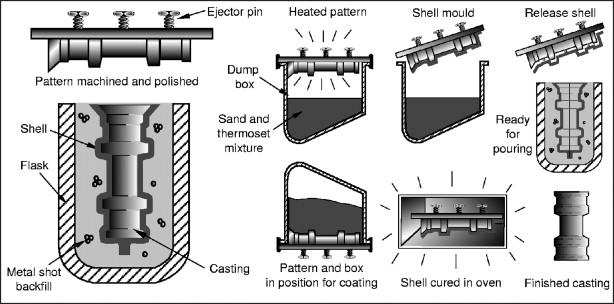