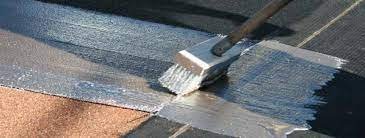
With all the convoluted jargon surrounding roof coatings, it’s critical to understand the benefits and drawbacks of different materials so you know what kind of coatings precisely is required for the job. Many of our items are labeled “fibered” or “non-fibered.” While this appears to be straightforward, it can be difficult to know whether to employ one over the other. We add cellulose or fiberglass fibers, solvents, and other ingredients to form a fibered product with exceptional bonding and penetrating properties. Viscosity is also controlled with fiber. This viscosity stops coatings from flowing on pitched roof surfaces while ensuring appropriate film build. They also give internal coating reinforcement, which increases the dry coating’s strength and aids in bridges and sealing hair-line fissures, so, with all of these benefits to adding fibers to a product, why would anyone use one that isn’t?
The only advantage of a non-fibered material is that it will extend out more on a roof, using less material. Because it is thinner, it does not provide as much protection. We prefer fibered to non-fibered products since the benefits outweigh the costs. Whereas a non-fibered solution may be less expensive, its protection is inferior to that of our fibered products. You will receive protection that can last lengthier than a non-fibered pail by spending a few dollars extra for every pail you use, and you will save money in the long term.
NON-FIBERED VS. FIBERED
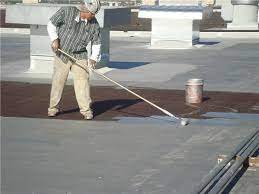
Understanding the key differences between the fibered and non-fibered roof and foundation coatings is critical. As you might expect, fibered coatings have more fibers than non-fibered coatings. Fibered coatings have added fibers that strengthen their strength while also controlling the fluidity (thickness) of the solution. This is significant because the lower the fluidity, the less likely the coatings will run.
WHAT IS THE PURPOSE OF FIBERED ROOF COATING?
Fibered Roof Coating is created to give exceptional weathering protection on most roof surfaces. It can be used as a protective layer over smooth finish BUR, SBS bitumen membrane, metal roof surfaces, and roll roofing.
WHAT IS A NON-FIBERED COATING, AND HOW DOES IT
WORK?
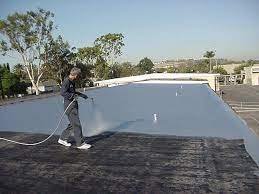
A non-fibered roof treatment does not include injection of fibers, as the name implies. When cured, non-fibered coatings have greater elasticity and stretching capabilities, but they may not be as resistant to tears and abrasions as fibered coatings.
FIBERED OR NON-FIBERED COATINGS ARE THE MOST EFFECTIVE
Because both treatments have their uses, the answers to these questions are genuinely dependent on the intended application. The type of ceiling, the total surface space, and the temperature and climatic factors to which the roofing may be exposed are all factors to consider.
IS A FIBERED ROOF COVERING WATER-RESISTANT?
The rubber and supporting fibers in this liquid sprayed asphalt coating produce a robust, flexible, and watertight seal.
WHAT MAKES UP A NON-FIBERED ALUMINUM ROOF COATING?
Non-Fibered Aluminum Roof Coatings comprises fine aluminum flakes, refined solvents, and chosen asphalts. When the paint is applied, the aluminum flakes fall in multiple parallel layers on the roof, providing a reflective, metallic barrier over the base material.
WHAT IS THE BEST WAY TO APPLY NON-FIBER ROOFING COATING?
Pour a tiny amount of the liquid coating over one piece of roofing and apply it with a roller into a thin, even covering. Allow the coating to dry for up to 24 hours before attempting to climb onto the roof.
REQUIREMENTS FOR COATING A ROOF
Choosing the appropriate roof coating is merely the first step. Managers must also consider weather conditions when applying a coating. Weather forecasts are important in determining when and where to apply roof treatments to get the best effects.
Temperatures should be at least 40 ° c at the time of the application, with one manufacturer suggesting 50 degrees. Managers should also check that the product has already been preserved in a moist, warm place, at minimum room temperature.
Managers should use the product when there is no chance of rain for the next 24-48 hrs after the application, allowing enough time for curing. Problems could also emerge if the roof’s surface temperature is higher than the base at the time of application.
Ponding water, curing durations, and weather are all factors that managers must consider because the foundation product that is spread over the priming and in between coats requires curing time. People don’t always consider the chilly temperatures when applying coatings. They consider the daily high temperature rather than the average temp (at the moment of the application) or the degree of the base at the time of application. They should think about how cold it was the night before. A maximum temperature is also set. It may glow too quickly if it’s too hot.”
Manufacturers must also consider the time of year the application is scheduled and the present meteorological circumstances.
“When deciding on a roof coating, It is important to consider the time of the year,” explains a roofing specialist. “Water-based coatings require sufficient curing or drying time to prevent the substance from washing away. Water-based applications start later in the winter or fall since the sun is out longer and sets earlier than at other times of the year. This may lengthen the project and increase installation costs.”
Windy conditions provide a risk solely during the application process when spray-coating particles can be transported into a parking area or carpeted area below.
“You can’t just put the spray painting down in any conditions,” Marzahl explains, “but once sprayed, the coating will work very well in hot, rain, snow, hail, or whatever.” “There are no problems once it’s administered and cured.”
WHICH ROOF COATING IS THE BEST?
Polyurethane coatings beat all other coatings in impact durability and foot traffic. The two types of polyurethane roof coverings are aromatic and aliphatic. These products are normally applied after a base layer and before a topcoat.